Anleitung Form 2
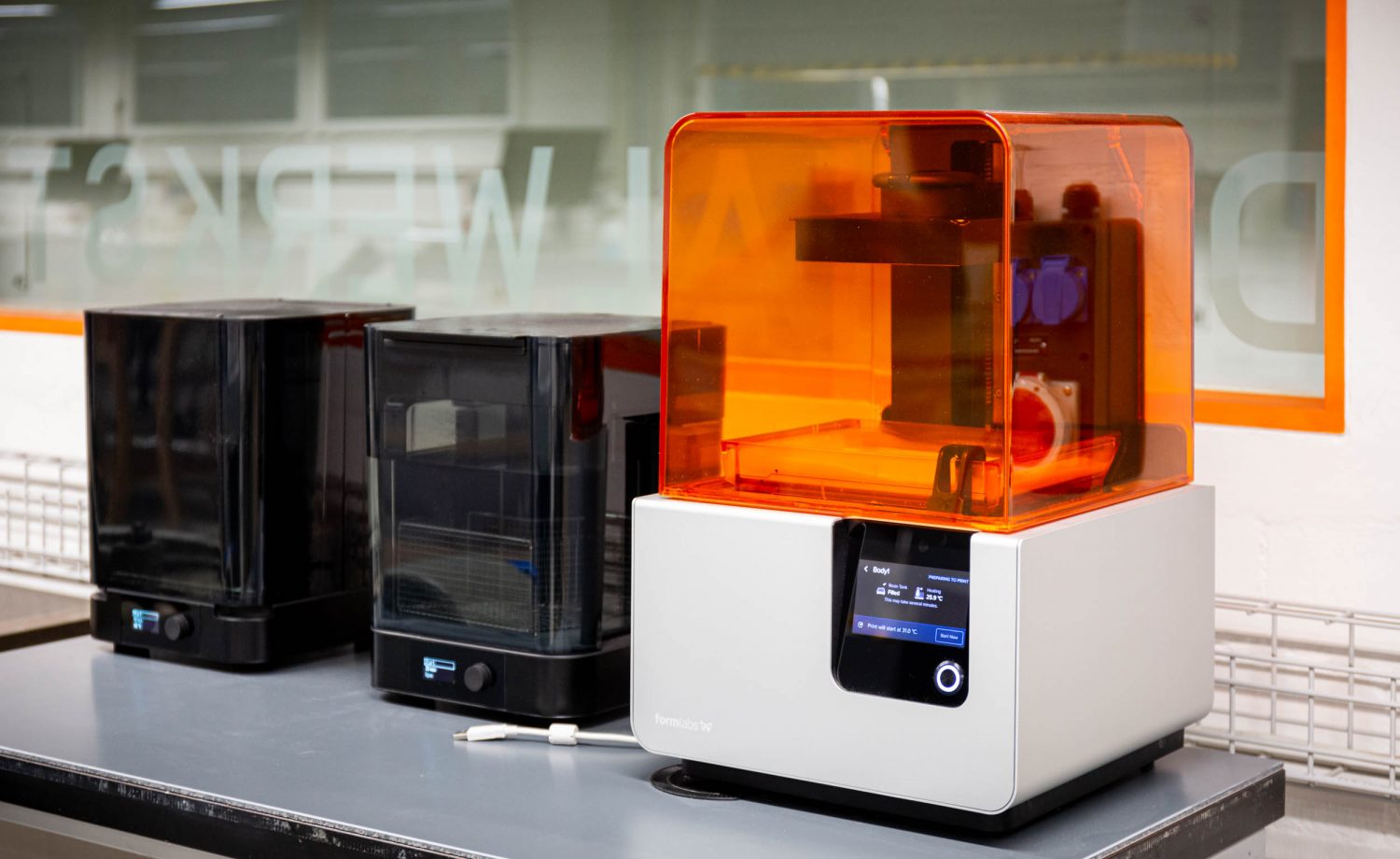
Maximale Druckgrösse: 145 x 145 x175 mm
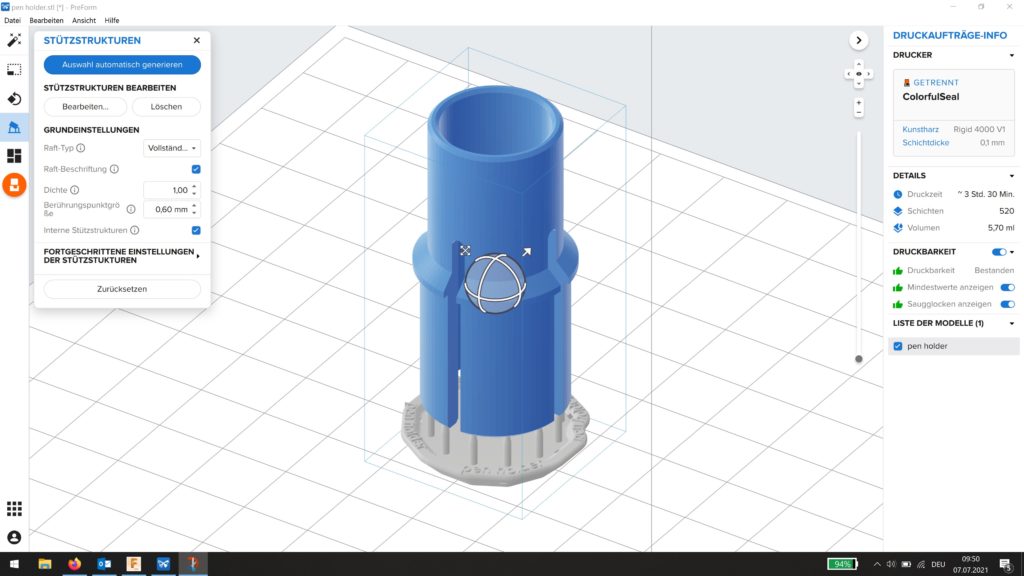
Schritt 1: Druckprozess
- Steckerleiste am Strom anschliessen
- Preform auf privatem Laptop öffnen
- Drucker nach Aufstartprozess mit Laptop verbinden
- Drucker- und Materialtyp sowie Auflösung definieren
- STL Datei importieren
- Druck automatisch einrichten (Zauberstab) oder manuell Stützstruktur hinzufügen
- Druckauftrag hochladen
- Print am Drucker drücken
- Lüftungsventil beim Harztank öffnen
- Druckplattform überprüfen
- Druck starten
Schritt 2: Reinigung
- Kontrolliere die Isopropanolmenge im Waschbecken. Der Füllstand sollte
zwischen den beiden Pfeilen sein. Kontaktiere einen Raplab Mitarbeiter,
falls er zu tief ist. - Wähle im Menu des Isopropanolbad die Funktion “Open”
- Entferne (mit Handschuhen) die Druckfläche
- Schliesse das orange Gehäuseabdeckung des Druckers, damit der Harz nicht aushärtet
- Entferne den Harz rund um das Teil mit einem Papier.
- Befestige die Platform in der Halterung vom Isopropanolbad
- Wähle die Dauer (10min bis 20min)
- Starte den Waschvorgang
- Kontrolliere, dass das gesamte Teil im Isopropanol eintaucht.
- Mehr Infos: Form Wash
- Reinige die Druckfläche mit Papier und Isopropanol
- Während das Teil gereinigt wird, kannst du bereits den Form Cure einstellen und aufheizen lassen.
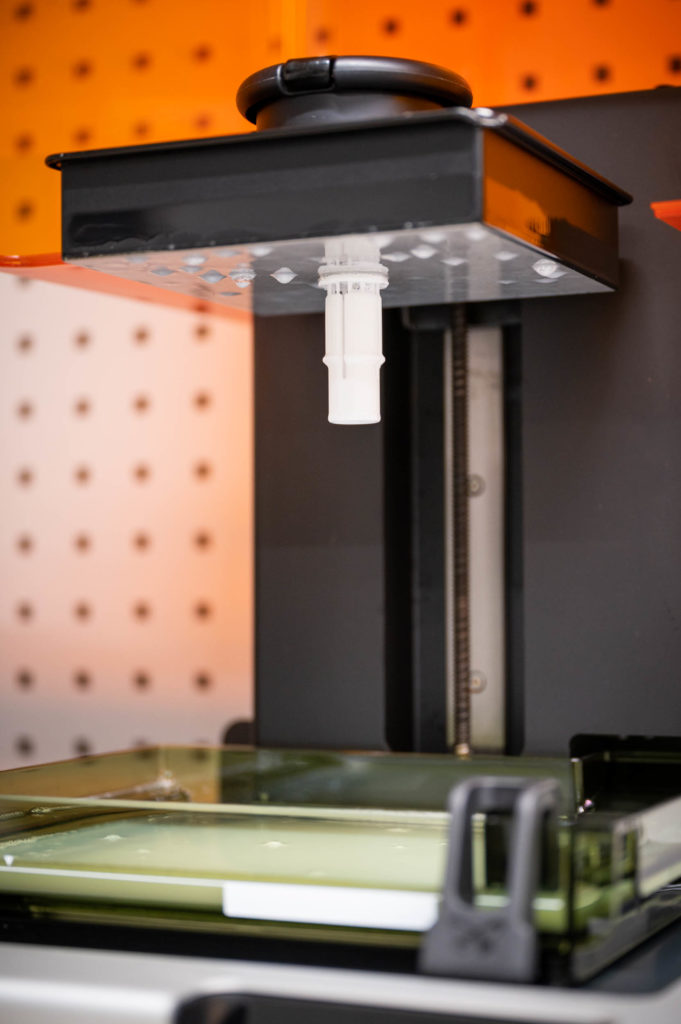
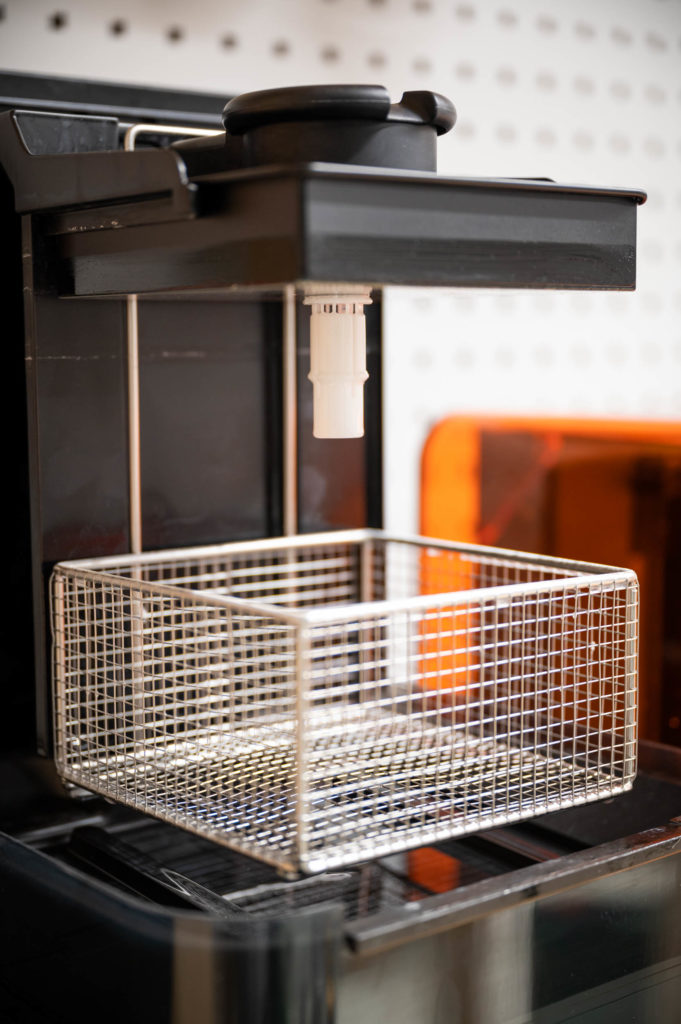
Schritt 3: Härten
- Platziere (mit Handschuhen) das Werkstück im Form Cure Gerät
- Wähle die Dauer (30min bei 60°)
- Mehr Infos: Form Cure
- Entferne die Stützstruktur mit Schleifpapier oder einer Feile
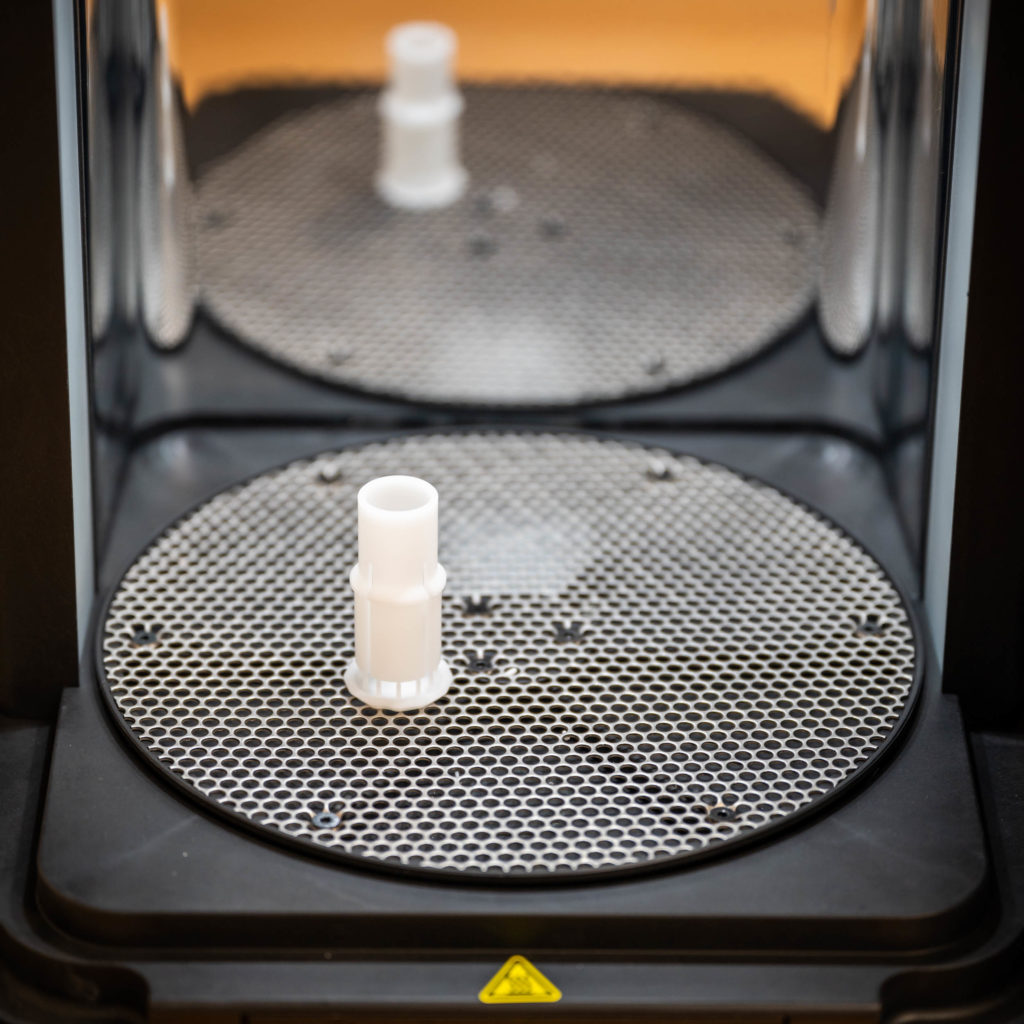
Schritt 4: Ausschalten
- Schliesse das Lüftungsventil vom Harztank
- Entferne die Stromzufuhr
- Reinigung aller Flächen (Gehäuse, Tisch) (nicht mit Isopropanol)