Scroll Band Saw
Introduction
Scroll Bandsaw Overview
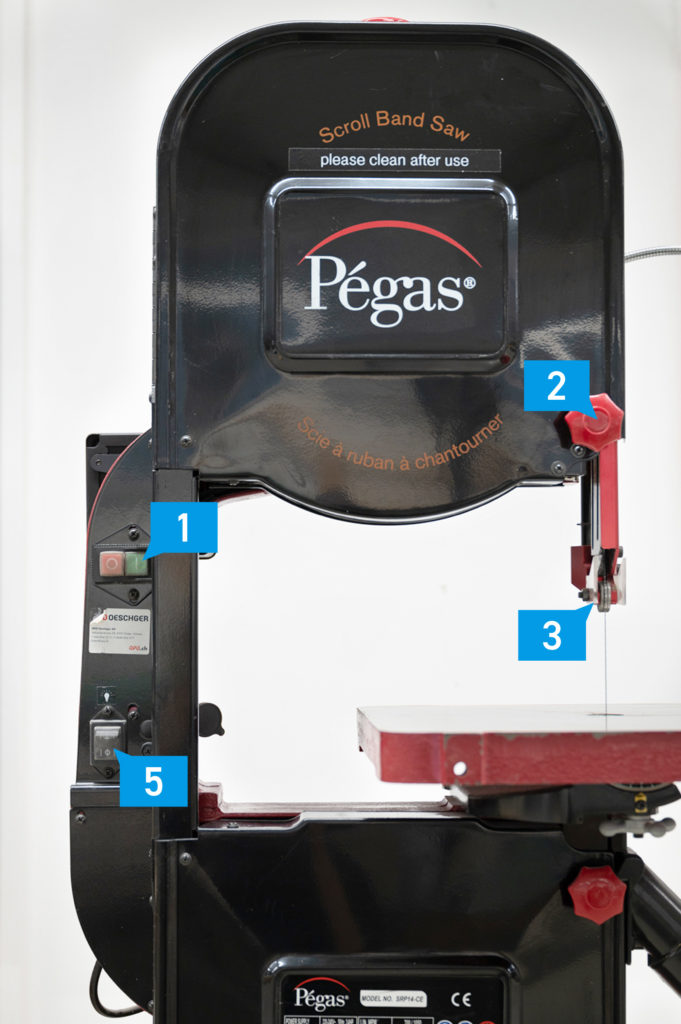
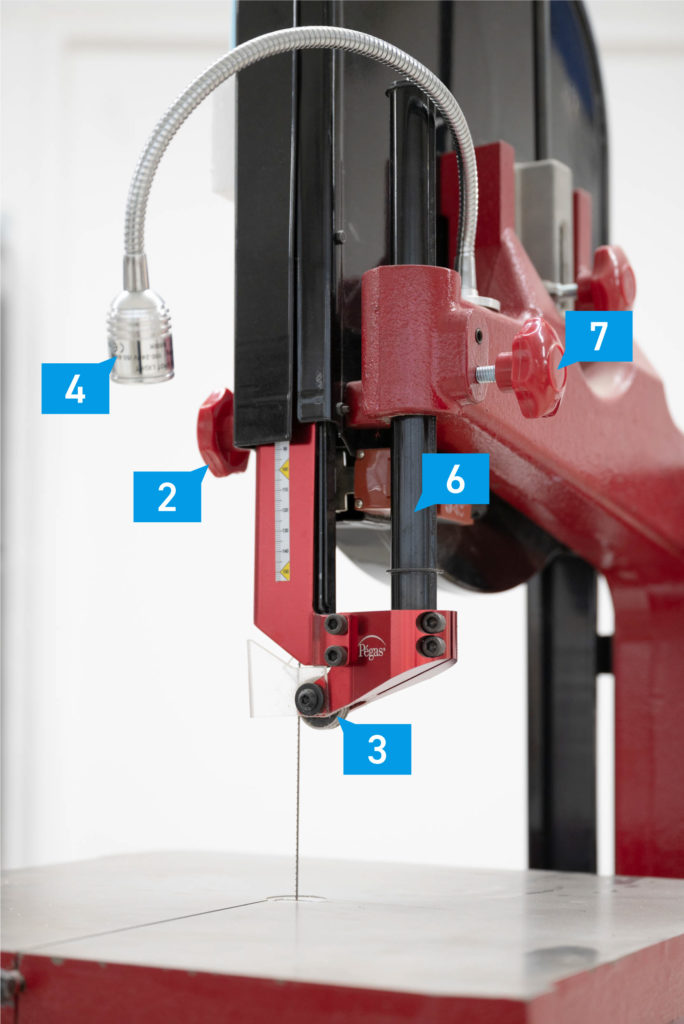
#1 Power switch
#2 Wheel for adjusting guide hight
#3 Guide assembly
#4 Light
#5 Light power switch
#6 Guide post
#7 Guide post lock
Preparation
Before you turn on the machine, set the guide assembly to the correct height. It should be no more than 10mm above the workpiece. As the picture shows, the scroll band saw can cut materials up to 100mm in thickness. This ability depends on the hardness of the material – remember that a piece of oak (high density and hard) is different from basswood or styrofoam (low density and soft)!
The scroll bandsaw works best for intricate curves and detail work; resawing stock and straight cuts is a task for the bandsaw and should not be attempted with the fine blade of the scroll bandsaw.
How To
Part of the safe working procedures of every woodworking machine is to keep the workpiece flat on the machine table and guide it with both hands at a safe distance to the cutting edge (100mm). Remember to use push sticks and other helping devices if the workpiece gets too small. Apply gentle pressure to avoid blade deflection.
Acceptable Materials
Available Machines
1 machine available
- Cutting width: 330mm
- Max. hight: 150mm
- Table size: 400mm x 400mm
Work Safety
- Cuts from pushing the workpiece by hand
- Cuts from not correctly adjusting the blade guard
- Injury from breaking the saw blade
Work Safety
- Never work from behind the bandsaw, pulling the workpiece
- Use only light pressure
- Turn off the machine before pulling back the workpiece
- The workpiece must rest on the table at all times
- Always support your workpiece on the machine table
- Take the toughness of the material into account before attempting to cut thick stock
Summary
The scroll bandsaw is a specialized machine for cutting tight curves in materials up to 100mm thick with a very minimal kerf. Its slow cutting speed enables you to cut materials like EPS and XPS (Styrofoam). It, therefore, becomes an alternative to the smoke-producing hot wire cutter. You must carefully consider the hardness of the material you want to cut since the machine is a delicate tool made for softer materials only.